In industries spanning printing, packaging, textiles, and manufacturing, the presence of defects in materials poses not only financial losses but also reputational risks. Enter web inspection systems, pivotal tools dedicated to identifying defects in continuous materials like paper, textiles, and films. Among the most groundbreaking advancements in these systems is the integration of automated defect detection, heralding improvements in accuracy, efficiency, and overall production quality.
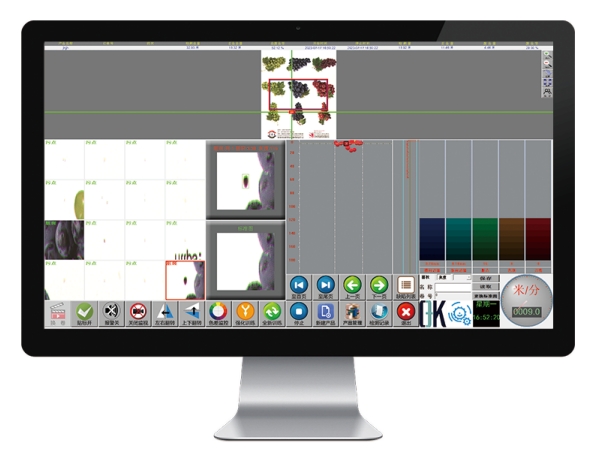
Understanding Web Inspection Systems:
Web inspection systems serve as specialized machinery deployed to scrutinize continuous materials, or "webs," for defects during manufacturing processes. These flaws can range from minor imperfections to critical errors rendering the product unfit for use. Traditionally, visual inspections by operators were the norm, but this method is susceptible to human fatigue and subjectivity, proving inefficient for high-speed production lines. Enter web inspection systems, armed with various technologies like cameras, sensors, and image processing algorithms, capable of accurately and swiftly detecting defects.
Automated Defect Detection: A Game-Changing Innovation
Automated defect detection marks a monumental stride forward in quality assurance within web inspection systems. Harnessing the prowess of artificial intelligence, machine learning, and computer vision, these systems swiftly and accurately identify defects in real-time, curtailing production downtime and waste.
Benefits of Automated Defect Detection in Web Inspection Systems:
Improved Accuracy: Automated defect detection systems utilize advanced algorithms and machine learning techniques to pinpoint defects with unparalleled precision. This precision ensures the detection of even the most minor imperfections, often overlooked by human inspectors, leading to the production of higher-quality goods.
Enhanced Efficiency: Unlike manual inspection methods, which are labor-intensive and time-consuming, automated defect detection systems can inspect materials at high speeds without compromising accuracy. This capability enables manufacturers to maintain efficient production rates and meet stringent deadlines while upholding rigorous quality standards.
Consistency: Automated systems offer consistent performance over extended durations, eliminating the variability inherent in human inspectors. This consistency guarantees uniform quality across all production batches, mitigating the risk of defects slipping through the cracks and reaching consumers.
Cost Savings: Early detection of defects in the production process translates to reduced waste, rework, and scrap costs. Moreover, preventing defective products from entering the market minimizes the potential for expensive recalls, warranty claims, and damage to brand reputation.
Real-time Monitoring: Automated defect detection systems provide real-time feedback on material quality, empowering manufacturers to promptly identify and rectify issues. This proactive approach averts defects from snowballing into larger problems, thereby minimizing production downtime and maximizing yield.
Data Insights: These systems generate invaluable data insights that can be leveraged to optimize production processes and bolster overall quality. By analyzing patterns and trends in defect occurrence, manufacturers can pinpoint areas for improvement, refine product designs, and enhance manufacturing practices.
Adaptability: Automated defect detection systems boast easy configurability and adaptability to accommodate diverse materials, production environments, and inspection requirements. This flexibility ensures effective defect detection across a broad spectrum of products and applications without necessitating extensive reprogramming or reconfiguration.
Technologies Underpinning Automated Defect Detection in Web Inspection Systems:
Automated defect detection relies on a synergy of cutting-edge technologies to accurately identify and analyze defects in continuous materials:
Machine Vision: Cameras, sensors, and optics capture high-resolution images or videos of the material under inspection, which are then processed using specialized software algorithms to detect defects like surface irregularities and color variations.

Artificial Intelligence (AI) and Machine Learning: AI algorithms, particularly those underpinned by machine learning techniques such as neural networks, analyze vast datasets containing examples of defects and non-defective materials to recognize patterns and anomalies indicative of defects.
Deep Learning: Deep neural networks, a subset of machine learning, automatically extract features from images and learn hierarchical representations of defects, enabling the detection of defects with exceptional accuracy across diverse materials and production environments.
Image Processing Algorithm: These algorithms extract relevant information from captured images, enhancing defect visibility by isolating defects from background noise or variations in lighting conditions.
Sensor Integration: In addition to visual inspection, web inspection systems may incorporate various sensors to detect defects based on physical properties like thickness, color, or chemical composition, enhancing defect detection capabilities.
Data Fusion: Data fusion techniques integrate information from multiple sensors and sources to improve defect detection reliability and accuracy, overcoming limitations associated with individual sensing modalities.
Connectivity and Integration: Modern web inspection systems feature connectivity features facilitating seamless integration with other manufacturing equipment and enterprise systems, enhancing workflow automation and decision support.
Challenges and Solutions in Automated Defect Detection:
Variability in Defect Types: Diverse printing processes and materials yield a broad spectrum of defect types and characteristics, necessitating the development of universal detection algorithms.
High-Speed Inspection Requirements: Web printing processes operate at high speeds, demanding defect detection algorithms capable of swift and accurate processing.
Complex Backgrounds and Patterns: Complex backgrounds and patterns in printed materials can confound defect detection, requiring advanced image processing techniques to distinguish defects from background noise.
Variations in Lighting and Contrast: Inconsistent lighting conditions and contrast across the web can obscure defect visibility, necessitating adaptive imaging techniques to enhance defect detection.
Large Data Volumes and Storage: Web inspection systems generate vast amounts of image data, posing challenges for data storage, management, and processing.
Defect Classification and Prioritization: Not all detected defects are equally critical, necessitating the development of classification algorithms to prioritize defects based on severity and impact.
Integration with Production Workflow: Seamless integration into existing production workflows and control systems is vital for real-time defect detection and process optimization.

In Conclusion:
Automated defect detection stands as a revolutionary force in quality control across manufacturing industries reliant on continuous materials, empowering manufacturers to deliver products of unparalleled quality and reliability. As the industry embraces automation and digitalization, automated defect detection will play an increasingly vital role in ensuring excellence across all facets of manufacturing.
Share this page with your family and friends.